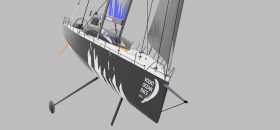
Wenige Monate nach der Ankündigung einer neuen, spektakulären Einheitsklasse für das nächste Volvo Ocean Race rund um die Welt, das in knapp zwei Jahren startet, geht der Bau der Volvo Ocean 65 bereits in Riesenschritten voran.
Die italienische Werft „Persico“ laminierte schon die Außenhaut des ersten, knapp 20 Meter langen Rumpfes, während bei „Multiplast“ in Frankreich die erste Karbonschicht für das erste Deck fertiggestellt wurde. Der Stapellauf ist im Sommer 2013 geplant.
Mit einer Gesamtlänge von 65 Fuß werden die neuen Rennmaschinen für die Regatta 2014/15 etwas kürzer sein als die vorherige Generation der Volvo Open 70. Dafür werden sie verlässlicher, robuster und erschwinglicher sein und dabei, so wie es Pat Shaughnessy von Farr Yacht Design ausdrückt, immer noch ein Grand-Prix-Rennboot mit höchster Qualität und einem coolen, ikonischen Design.
Mit ungefähr 4,5 Millionen Euro pro Boot werden sie etwa 30 Prozent billiger als die VO70 sein bei zudem geringeren laufenden Kosten. Dennoch ist die größte Änderung die Entscheidung zugunsten eines strengen Einheitsdesigns, ein Novum für diesen Event.
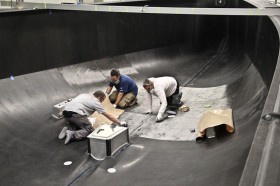
Während die Kampagnenbudgets durch die Lieferung von identischen Booten und Ausrüstung angeglichen werden und damit einhergehend noch spannendere Rennen zu erwarten sind, bedeutet die Entwicklung dieses neuen Grand-Prix-One-Designs zur Weltumseglung neue Herausforderungen für die Organisatoren des Volvo Ocean Race.
Die Kombination von bestechendem Leistungspotential vom Fleck weg mit einer Robustheit, die mindestens zwei Umläufe dieses strapaziösen Rennens übersteht, ist keine leichte Aufgabe. Genauso, wie die Schaffung einer Vorlage für eine Flotte von wegweisenden Grand-Prix-Booten. Jedes Detail dieses Projekts muss geklärt sein, bevor der Bauprozess startet. Wenn die Produktion einmal begonnen hat, ist es zu spät, um Details zu modifizieren.
Die Aufgabe, die neue Yacht zu entwickeln, wurde durch die Vielzahl von Orten in Italien, Frankreich, der Schweiz und in Großbritannien besonders erschwert, an denen unterschiedliche, wichtige Teile gebaut werden. Jedes Element muss sich passgenau in die finale Verarbeitung einfügen lassen, damit das Konzept funktioniert.
„Früher haben einige Teams Modelle von bestimmten Bereichen ihres Boots gebaut, bei denen die Ergonomie kritisch war. Aber für dieses Projekt haben wir bei Green Marine in Southampton ein Modell des Boots in seiner ganzen Größe errichtet“, erklärt Projektmanager James Dadd. „Dort werden die Rennyachten letztlich zusammengebaut.
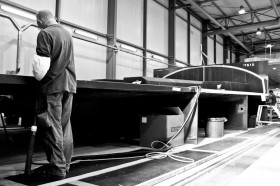
Das interne Modell erlaubt uns einen genauen Blick auf das Grundlayout an und unter Deck. So haben wir bei der Navigationsecke und der Kombüse sofort einige Details erkannt, die weitere Entwicklungen benötigten.“
„Die gesamte Kabelführung ist ein weiteres Beispiel, wie wichtig es ist, das Boot in seiner vollen Größe zu sehen. Wie die Kabel verlaufen sollen, und wie die Installation vonstattengehen wird, lässt sich am besten bei voller Größe herausfinden, besonders wenn die Kabelstränge später als Einheit für jedes Boot geliefert werden. Das Design der bedeutsamen Befestigungskonsolen für die Kommunikationsausstattung ist ein weiterer Schlüsselbereich, der vom Trockentest profitiert hat.“
„Das Schwenkkielsystem ist ein anderes Beispiel. Wir wollen nicht nur sicherstellen, dass die Kolben schnell einzupassen und leicht ausgetauscht werden können, wenn das Boot einmal gebaut wurde. Aber den Kielbolzen sechs Grad zu neigen, damit die Kielfinne Auftrieb erzeugt, wenn sie gekippt ist, kompliziert das Layout in der Mitte des Bootes und zieht woanders weitere Auswirkungen mit sich. Das in voller Größe zu sehen, macht es um vieles einfacher, zu kontrollieren, dass alles wie geplant funktionieren wird.“
„Wir wollen auch sicherstellen, dass Zugriffslöcher hierfür und für andere Details von Beginn an in der Form mit eingebaut sind. Dies sorgt nicht nur vielfach für bessere strukturelle Lösungen, sondern reduziert auch Kosten. Außerdem wird die Fertigstellung dieser Boote so eher zu einer Einbauarbeit, nachdem die Produktion angefangen hat. Idealerweise benötigen die Bootsbauer kein Maßband, um eines dieser Boote zusammenzusetzen.“
Doch die Kostenreduzierung ist nicht der einzige Vorteil dieses neuen Einheitsdesigns. Ausgehend von einem leeren Blatt Papier bedeutet, dass Bereiche des Boots, die früher von strikten Regeln bestimmt wurden, angepasst werden können, wenn das zu einem besseren oder effizienteren Weg führt. Dies kann oft zu Win/Win-Situationen für die Organisatoren und die Teams führen.
Als früherer Bootsmann für „ABN AMRO“ und Shore Manager bei „Puma“ und bei „Camper“ in den vorigen beiden Rennen verfügt Neil Cox über viel Erfahrung bei Bau, Betrieb und Reparatur von Volvo-Booten: „Wir wussten aus Erfahrung, dass die Volvo Open 70 im vergangenen Rennen von nur 40 Kilogramm Extra-Struktur profitiert hätten, aber wir konnten es nicht umsetzen, da es das Regelwerk nicht erlaubte. Dieses Mal können wir solche Änderungen ohne Probleme vornehmen, da sie auf jedem Boot zum Tragen kommen werden. Von einem robusten Boot, das härter gefahren werden kann, profitiert jeder.“
Die Segel sind ein weiterer Bereich, in dem das Einheitsdesign Vorteile bei Komplexität und Kosten bringt. „Jedes Team wird die gleichen neun Segel haben, darunter eine Sturmfock und ein Trysegel“, erklärt Regattaleiter Jack Lloyd. Die Segel werden zusammen mit dem Boot ausgehändigt. Für das Rennen bekommen die Teams dann zum Start in Alicante noch einmal sieben weitere Segel. Keines dieser Segel kann von den Teams modifiziert oder repariert werden, mit Ausnahme vom Vermesser genehmigter Maßnahmen, wenn ein Segel beschädigt wurde.
„So ein striktes Einheitsdesign zu entwerfen, ist zehn Mal mehr Arbeit als die Entwicklung der früheren Box-Regeln, da wir jede vorgeschlagene Komponente überdenken müssen. Wir müssen sicherstellen, dass wir die geeignetsten Elemente für die Ausführung der Arbeit stellen, und dass sie in der Praxis auch funktionieren.
Mit einem einfachen Beispiel lässt sich überprüfen, ob die Bolzenschneider, die wir zur Verfügung stellen, in den vorgesehenen Stauraum passen. Die Ausrüstung zu liefern, ist sicherlich einfacher, als Regeln darüber zu verfassen, was erlaubt ist. Ein genaues Modell ist daher von unschätzbarem Wert bei der Überprüfung dieser Details.“
Das Modell bedeutet auch, dass mehrere Zulieferer sich treffen konnten, um über den Zusammenhang zwischen bestimmten Komponenten zu diskutieren und vor Ort zu sehen, ob es Probleme gibt. Sobald der Produktionsprozess begonnen hat, steht das Modell den Teams zur Planung für ihr eigenes Boot zur Verfügung.
Die Fertigstellung des ersten Boots der Produktionslinie wird Ende Juni 2013 erwartet. Anschließend wird alle sieben Wochen ein neues Boot aus den Toren von Green Marine auslaufen. Der Plan ist, jedes Boot innerhalb von drei bis vier Tagen segelklar zu haben. Es scheint ein ambitioniertes Ziel zu sein, doch die neue Generation der Volvo-Boote ist bereit, ein weiteres Mal neue Maßstäbe zu setzen. Der Bau eines detailgetreuen Modells ist nur einer von vielen bedeutenden Schritten.
Schreibe einen Kommentar